«Сама по себе закалка стали – довольно распространенный и хорошо изученный процесс, описанный во многих умных книгах, но вот только описан он такими умными и непонятными словами, что обычные люди, такие как мы с вами, запутаются на второй странице и не вынесут для себя ничего полезного. Мы же поставили себе цель не запутаться и сойти с ума от обилия непонятных терминов и формул, а разобраться…» (Ю. Иванов «Азбука ножа»)
Сталь есть сплав железа с углеродом – это все знают. В нагретой до определенного момента стали углерод находится в растворенном виде. Сам углерод в сталь проникнуть не может, для этого ее надо нагреть докрасна в науглероживающей среде – это процесс цементации. Запомните это слово похожее на всем известное «цемент». Цемент (лат. caementum — «щебень, битый камень»)
Углерод можно добавить и в расплавленную сталь, как повар добавляет в суп специи. При получении стали из чугуна, углерод наоборот «вынимают» различными способами. Все это только для понимания того, что без углерода стали не бывает. То есть, любая сталь состоит из железа и углерода, плюс некие специи, которые добавил повар в этот стальной суп при варке.
Кстати, это очень точная аналогия, хотя и не моя. Когда у меня спрашивают, как и где я варю сталь, то довольно правдиво отвечаю: «На даче, в горшочке». Мне, конечно, не верят, думая, что шучу. Однако, если под дачей понимать расположенную за городом небольшую мастерскую, а за горшочек - шамотный тигель, то все остальное совершенно точно. И специи по ходу варки добавлять приходится, и помешивать иногда, и смотреть – готово или не готово мое варево.
Несколько лет назад в свет вышла книга «Азбука ножа» инженера-конструктора одного из уральских предприятий Юрия Иванова. В этой книге автор простым языком в форме дружеской беседы пытается представить читателю свой взгляд на теорию резания. Аналогия про повара из этой книги. Мне очень приятно, что я был консультантом при написании одной из ее глав. Позволю себе привести еще парочку интересных сравнений оттуда.
«Представим себе, что наш кусок стали состоит не из каких-то невидимых фигур, а, скажем, из тряпичных сумок, с которыми мы ходим в магазин за продуктами. Развесим эти сумки на веревку, одна за другой, рядом натянем еще веревку с сумками, потом еще и еще. Зрелище фантастическое – поляна, поле, целый аэродром затянут рядами веревок, на которых болтаются подвешенные авоськи. Мы можем подойти и смять каждую сумку, сложить ее пополам, вчетверо – как угодно, ведь это просто кусок материи. Даже простой ветер заставит эти сумки болтаться в разные стороны.
Теперь давайте представим, что кто-то огромный … в каждую насыпал доверху яблок или картошки… Теперь каждая сумка уже не просто бесформенная тряпка, а тугой раздувшийся мешок… каждую сумку со всех сторон подпирают такие же раздувшиеся соседи и все вместе они образуют нечто плотное и крепкое… Мы увлеклись фантазиями, но именно сейчас на наших глазах произошел процесс, который на языке специалистов называется закалкой стали… Чтобы не томить любознательного читателя, сразу скажу, что под развешенными на аэродроме сумками мы подразумевали мельчайшие частицы железа, картошка в этих сумках выступала в роли частичек углерода, которые каким-то образом смогли туда проникнуть, а весь этот картофельно-сумочный аэродром и есть кусок стали, внутри которого мы путешествуем».
Кому-то эта аналогия покажется не совсем подходящей, не спорю, но главное сделана попытка объяснить сложное простыми словами. А так как я уверен, что автор книги на меня не обидится, дам еще одну большую цитату. И то, что написано в ней очень важно уяснить, так как на этом процессе и основана закалка любых сталей.
«Для растворения углерода в стали наш слиток необходимо нагреть до определенной температуры (около 740…850 градусов) и выдержать некоторое время. Этот процесс очень похож на растворение поваренной соли в воде – в стакане очень холодной воды мы вряд ли сможем растворить даже чайную ложку соли, сколько бы ее ни перемешивали. Но если в этот же стакан налить кипяток, то в нем эта ложка соли без труда растворится за несколько секунд. Добавим еще ложку соли – растворилась, добавим еще – опять растворилась, еще и еще… В результате мы получим очень соленую воду, в которой соль уже не сможет растворяться, как бы мы не старались».
Причины и механизмы растворения углерода в стали, как и его выделения в определенных условиях, нам для закалки знать не обязательно. Древние мастера вообще не знали что такое углерод и градусы, однако сталь калили и, пишут, иногда очень неплохо получалось.
Замечу, что как бы мы не старались мы не сможем запихнуть в железо больше 6,67% углерода. Да нам столько и не нужно. Обычно производители ножей работают со сталями с количеством углерода в них 0,35..1,2%. Я лично с несколько большим - где-то 1,5…2,2%, но, как вы увидите ниже, серьезной разницы в закалке любых сталей нет, нужно учитывать только температуру нагрева под закалку, чтобы растворить как можно больше «соли» и скорость остывания.
«Если теперь мы оставим наш рассол спокойно остывать, то через некоторое время увидим, как соль начнет выпадать в виде кристаллов, и чем сильнее будет остывать наш стакан с рассолом, тем больше соли выпадет в осадок, то есть, при охлаждении вода в стакане будет становиться менее соленой, поскольку соль будет выделяться из воды и выпадать в стакан в виде кристаллов.
Давайте теперь попробуем охлаждать наш пересоленый кипяток не постепенно, а резко, чтобы он за несколько секунд превратился в лед. В этом случае мы не увидим никаких кристаллов выделившейся соли – она просто не успеет вырасти в кристаллы и выпасть в осадок, в результате чего мы получим очень соленый лед. К чему мы затеяли этот соленый эксперимент? Да к тому, что растворение углерода в железе, равно как и выпадение его обратно при медленном охлаждении происходит точно так же, как и соль в воде – природа этих процессов одинакова и изменить ее мы не в силах.
Отсюда следует простое правило – чтобы закалить сталь, то есть сделать ее более прочной и твердой, ее необходимо нагреть до определенной температуры, выдержать какое-то время (чтобы углерод успел полностью раствориться в железе) а затем резко охладить. Именно при резком охлаждении углерод не успеет выделиться из железа (картофелины не успеют повыскакивать из сумок) и наш будущий нож станет твердым и прочным».
Температура при которой в стали начинается растворяться углерод, называется критической точкой стали и обозначается Ас1. Вообще-то, слово «критическая» как-то путает и немного пугает, сразу представляется что-то опасное и неудобное. Поэтому для лучшего понимания определение «критические точки» проще заменить на «нужные точки». Это для стали они может быть и критические, а нам без них в закалке – никуда.
Эти нужные нам критические точки в 1886 году открыл наш соотечественник Д.К. Чернов, поэтому эти точки называют еще точками Чернова. Они всегда обозначаются буквой «А».
Первая нужная точка, (а критические, но нам не нужные, я постараюсь не упоминать), лежит на температурной линии в 727 градусов. Эту линии еще называют линией эвтектоидного превращения. Только для закалки эта линия нам особо-то и не нужна, поэтому позже заменим ее другой, пусть и не совсем критической, но более полезной.
Для понимания: эвтектика – это механическая смесь двух или более видов кристаллов, одновременно кристаллизовавшихся из жидкости (нашего солевого раствора). Так как из солевого раствора выделяется только один вид кристаллов, то никакой эвтектики там нет. Однако, если бы одновременно выпало в осадок еще что-то отличное от соли, допустим известь, то была бы и мы смогли бы начертить диаграму, а выпавшие кристаллы извести и соли у нас стали бы фазами.
Фаза - это то, что имеет четкую границу, то есть, - составляющая смеси, резко отличающихся от других составляющих.
Почему такая важная критическая линия PSK на диаграмме железо-углерод нам не нужна?
Да потому что мы редко имеем дело с чисто углеродистыми сталями, а легирующие элементы двигают эту линию по температурной шкале туда-сюда: одни ее повышают, другие понижают. Большинство, конечно, повышает, поэтому для каждой марки стали критические температурные точки - точки необходимого нагрева, когда в ней начинает растворяться углерод, и охлаждения, когда он выделяется – разные. Да и для закалки стали при нагреве температура должна быть немного выше этих точек, чтобы углерод растворялся активнее.
Для наиболее распространенных сталей закалочная температура находится в пределах 760-860 градусов, поэтому вторую нужную нам линию в нашей будущей закалочной таблице можно провести по температуре в 850. Это будет некая усредненная температура закалки.
Если рассматривать диаграму железо-углерод, то правая часть с чугунами нам не нужна. Не нужна и верхняя с расплавами, поэтому диаграмму спокойно можно урезать вот до такого вида еще и срезав ее до температуры 1100 градусов.
Но даже такая упрощенная схема нам мало поможет, потому как есть еще высоколегированные популярные у любителей ножей стали и их температура закалки не будет попадать в обозначенную на рисунке область закалочных температур. Поэтому придется поработать с новыми терминами для лучшего понимания процессов и начертить свою упрощенную но понятную закалочную схему для всех классов популярных ножевых сталей.
Сразу прошу прощения за то, что вряд ли смогу обойтись без специальных терминов, но что поделать – структуры стали и закалка даже сейчас остаются великим колдунством. Например, при одной и той же температуре закалки некоторые стали могут закалиться, а могут и не закалиться вообще. Дело здесь в направлении закалки – снизу вверх или сверху вниз по температурной шкале. То есть, нагреваем мы сталь до нужной нам температуры, или остужаем ее.
То, что углерод растворяется – это непонимания, думаю, не вызывает. А вот на слова что он выделяется, сразу возникает вопрос: «в каком виде?».
Углерод выделяется в виде его соединения с железом в форме карбида железа – Fe3C. Это самая твердая фаза, какая может только быть в стали. Называется она цементитом, видимо от того, что под микроскопом похожа на битые камни, в вязкой перлитной матрице. Но это не точно. Проскочило слово «перлитной», так вот «перлит» - это основная, ключевая фаза большинства сталей. Состоит перлит из феррита (железа) и цементита – карбидов железа.
Здесь все очень просто – все стали состоят из феррита и цементита, потому как больше не из чего. То есть, если простыми словами, все стали состоят из железа и соединений углерода с ним. А разные структуры получаются по причине дисперсности (измельчения) этих структур и формы соединений углерода.
Проще всего представить перлит можно в виде цементно-песчаной смеси, где связующее - цемент выступает в роли железа, а песок в виде цементита – Fe3C. А так как песок может быть мелким, крупным по фракции, то и названия таких смесей разные, хотя основа одна – цемент и песок.
Помимо мелких частичек и чешуек цементит может образовывать крупные карбиды – камушки или, если принимать во внимание его большую твердость и хрупкость, «алмазы». Скопления карбидов и выглядят под микроскопом как скопление маленьких блестящих алмазиков. Если в нашу цементно-песчаную смесь добавить немного щебня, это и будет очень похоже на структуру такой стали – перлит плюс цементит.
Надеюсь, всем понятно, что количество, размеры, форма нашего «щебня» очень сильно влияют на свойства получаемого «бетона» или стали в нашем случае? Если щебня не очень много – свойства мало будут отличаться от свойств цементно-песчаной смеси, если только один щебень, а смеси мало, то наш бетон будет очень хрупким, хотя и твердым.
Есть в стали цементит в виде карбидов (битый камень) или нет, очень важно знать для определения режимов закалки и получения нужных нам свойств. Приправы в виде легирующих элементов изменяют свойства карбидов, делая наш щебень более тугоплавким и более твердым. То есть, изменяется состав карбидов – он усложняется, и изменяются свойства нашего связующего железа. Если проводить аналогии, то с добавлением легирующих в сталь (бетон) наш цемент становится не трехсотой марки, а пятисотой, только и всего. И при этом щебень стал прочнее – из мрамора с твердостью 6 превратился в кварц с твердостью 7 по Моосу.
В так называемой «алмазной стали» нет никаких алмазов, но зато там много легированных вольфрамом твердых карбидов, которые упрочняют мартенсит. «Мартенсит» - еще одно слово, которое надо запомнить. Это собственно та структура, которую нам нужно получить при закалке. Это структура представляет собой не песчано-цементную смесь, а наш замороженный лед – твердый раствор углерода в альфа-железе, часто в перемешку с битым камнем – карбидами.
Я написал твердый раствор в альфа-железе специально, чтобы потом сказать, что бывает еще один твердый раствор – раствор углерода в гамма-железе. И это важно, потому как раствором в альфа-железе мы режем, а с раствором в гамма-железе работаем при закалке. Ну, такое вот оно железо – при нагревании меняет свои свойства и кристаллическую решетку. Есть еще и бета-железо, и хотя про него говорят мало, как важный элемент закалки оно нам понадобится.
Итак, пока мы знаем основные фазовые составляющие стали, состоящие из разнокалиберного железа и углерода: перлит, цементит, мартенсит. Чтобы закалить сталь, нам нужно из смеси железа и углерода – перлита или перлита с цементитом, получить твердый раствор углерода в железе - мартенсит. Из цементно- песчаной смеси с гравием сделать очень соленый лед. А для этого, как вы помните, нужно просто нагреть сталь до определенной температуры.
Причем нужно понимать, что нагрев стали под определенную температуру и остывание стали до этой температуры приведет иногда к совершенно разным результатам при закалке. И диаграмма железо-углерод (цементит) нам в закалке поможет не много, так как она описывает идеальные условия: изменения в углеродистых сталях при очень медленном нагреве. Поэтому ее проще забыть и нарисовать свою закалочную таблицу, ориентируясь при этом не на термопары и муфельные печи, а на тысячелетний опыт мастеров работающих со сталью.
Эта часть рассказа о закалке вышла какой-то уж слишком фантазийной по причине множества аналогий, зато следующая будет сугубо практической с минимумом определений и сравнений. Но это не точно. Добавлю только еще один термин, чтобы читатель мог понимать и представлять процессы, происходящие в стали. Хотя можно обойтись и без всего этого, как обходились без знаний о фазах и структурах наши предки. Определить углеродистая перед вами сталь, легированная или нержавеющая довольно просто. А это необходимо знать перед закалкой.
Комментарии
Пасиб, в закладки🤗, однозначно.
Но есть ещё и отпуск😎🤐.
И да, я топоры(65 г) чуть перегревал похоже, хотя потом приотпускаю их, вроде рубят,народ доволен.
И длинный ( типа вакидзаси))ножик себе из торсиона ( мерседес, но аналоги нашей 65г,походу)) сделал- пластичный, и на жезке зазубрины оставляет, правда я его слегка подвёл, не до " бритвы".🤗
О нем потом. Как же без него.
15 лет отработал на Ипсенах немецких,Чиффах итальянских,там программу вбил,садку в предкамеру загнал
,дальше все автоматика и на компьютере можно все проследить. А так спасибо за ностальгию
.
Да не за что). Правда был случай, сварил слиток сделал полосу, поковку заказчик выточил нож и отдал на завод закалить. Завод крутой ВПК, но они не могут. Печь запрашивает марку, а откуда ей взяться, если на глаз варил. В общем пришлось долго обьяснять, как закалить без компьютера.
Вот, так и живём- искра на наждаке, и чуйка при нагреве( пирометра нету((
Да такая ерунда в термичках аля Путиловский завод 1917 год,принесут болванку,сталь такая та,надо твердость такая та,по итогу сталь ни такая та.И начинаються танцы с бубнами
Я сразу скажу, без обид, ладно? Ничего личного. Просто выскажу свое личное мнение, краем уха - уголком глаза - пальцем левой ноги имевши некоторое отношение к пресловутому ВПК.
Описывать технологии тысячелетней давности - это прикольно, но сродни стимпанку. Во-первых, это красиво, а во-вторых вроде как и не придумывается ничего больше.
А знающим людям вместо этого правильнее было бы петь оду технологиям современным.
Это когда сплавы, которые называют прецизионными, имеют по 6-10 легирующих примесей и контролируются в процессе производства детали по 15-30 различным химическим элементам.
Это когда диаграмма состояний напоминает лоскутное одеяло, а для путешествия по нему термообработка и механическая обработка идет в несколько циклов, перемежаясь с химической обработкой типа цементации в газообразных парах метанола.
Это когда полученное изделие с толщиной стенки в 1 мм выдерживает такое же давление, как стальная труба с сантиметровой стенкой. Весит меньше = летит дальше.
Это когда на детальное исследование узкоспецифичных составов потрачены не человеко-часы, а человеко-жизни. С достижением поставленных целей, что характерно.
Это когда, имея три десятилетия для исследований, американцы не могут скопировать ракетный двигатель, а китайцы - турбореактивный. Потому как, имея на руках точнейший химический состав отдельно взятой железки, не в состоянии понять, как эта адская смесь была сварена.
Поэтому уважаемый автор слегка ошибся аудиторией. Просвещать доступными словами надо бы не мужиков среднего возраста, которые уже доросли до контента афтершока, а детишек лет 12-15, для того, чтобы кто-то из них поступил в МИСИС или другие профильные ВУЗы, и смог бы в перспективе встать на смену тем, кто несет настоящие знания и технологию на своих плечах сейчас.
Так здесь про ножи и ХО. Заметили, что я специально много разэто подчеркивал. С другой стороны при всем уважении к тем заводским термистам, удивляет что не нашлось ни одного, способного соственноручно нагреть сталь до светло-красного цвета).
Хотя это другая тема, про то, должен ли уметь держать напильник, хороший оператор станка с чпу))
В этом-то и весь вопрос. Про погоду, очевидно, уместнее рассуждать на сайтах о погоде. Ну а про ножи - на ножевых форумах.
Я добросовестно надеюсь, что своими статьями, кроме как повысить свои продажи, вы хотите показать аудитории афтершока что-то хорошее, доброе, вечное. Но вот что именно?
Повысить продажи,конечно.
Уже выросли, только может подскажете где?) Да и попробуйте заказать еще)
А про заводы на заводских, аипро армию на армейских, про медицину на медицинских.
Если бы я хотел что-то продать, то выступал бы под своим именем и давал ссылки на то место, где что-то можно купить. Так?
А несу ли я доброе и вечное в массы, скажут читатели и подписчики. Впше мнение одно из многих.
Я ведь просил вначале, без обид.
Я сам скажем так человек науки, поэтому любые человеческие знания считаю так или иначе полезными. Поэтому не имею ничего против вашего ликбеза даже в приложении к узкой ножевой теме. Но вот что меня смущает.
Нож - это если оружие, то сугубо индивидуальное. Хорош тем, что его может сделать любой рукастый мужик (конечно, приложив некоторые знания и навыки). Но современные войны не выигрываются ножами. Современный уровень - это всякие летающие в атмосфере или висящие в космосе штуки.
Двое людей всегда могут сделать вместе больше, чем сумма отдельных человеческих возможностей. Сто мастеров, объединившись в мануфактуру, могут сделать в сотни и тысячи раз больше, чем сто отдельных кустарей. Сто мануфактур/артелей/заводов, объединив усилия, как раз оказываются в состоянии делать всякие летающие штуки, в то время как сотня тысяч кустарей смогут делать только сотню тысяч ножей.
Что в данный момент актуальнее, нам покажет история. Ждать, кстати, недолго.
Об этом у меня в прошлых статьях. Я везде где можно объясняю (надоел уже наверное с этим), что разделение труда в производстве повышает и качество и количество продукции. Кустарей делающих сложный по технологиям продукт с нуля - не было.
А в чем собственно наши с вами разногласия? Я их пока не увидел.
Наверное, в том, что сейчас думать надо не о ножах. Если актуален нож - значит, враг на расстоянии вытянутой руки, значит, никого из своих нет ни рядом, ни за спиной. У нас действительно все так плохо?
Ножевое дрочево (извиняюсь за грубость) характерно для подросткового возраста и сродни идеологии выживальщиков, типа, все умрут, а я останусь. В реальности же рулит максима "разделяй и властвуй". Одиночки не выживают.
Даже у Наполеона было хобби. Зациклинность на политике или на конце света - есть мания. Или фобия, это надо у знающих уточнить.
Кажется, Вы зациклились на том, что нож - это непременно оружие.
У меня вот лет 20 как постоянно с собой складничок. Последние лет 10 вот этот прижился. Прямое лезвие, замок лайнер, рукоять ухватистая - большего и не надо. Ну, разве что клипсу, а то в джинсах постоянно 2 дырки протирает поверх кармана. Да, дешевенькая китайская нержавейка, легко садится, легко правится. Но под мелкие повседневные задачи - вполне хватает.
А вот с этого места подробнее, пожалуйста))
Ну тогда и вы тоже без обид...
Почему-то ни один "гений" никогда сразу не вкуривает, к чему приведут их гениальные изобретения, включая ммм.., как там у вас..? - Далеко летающие, легированные 3-мя десятками примесей, тонкостенные трубы...
А приведут они ровно к тому, что рано или поздно, статьи типа этой, окажутся чрезвычайно актуальными, если не сказать единственно актуальными, как в смысле доступных технологий, так и в смысле банального выживания...
Так что обывателю намного полезнее знание устройства ветряной мельницы XVI века, чем ультрасовременного ветряка...
Специалистов на заводах отучили от кустарщигы в 30-х, хотя они и сильно сопротивлялись. Потребовалось вмешательство с самого верха. Собственно в этом отличие специалиста от кустаря: один полагается на знания, а другой на интуицию и опыт.
П.С
Не вы говорили, в одной из прошлых публикаций, что из метеоритного железа хороший нож не получится?
Смотря что вы понимаете под хорошим ножом) А то вот в прошлой статье я как раз писал про это недопонимание). Кстати, из какого такого метеоритного железа? Там на небесах нет ОТК с ГОСТами. Иногда там серы с фосфором столько, что лучше ничего не делать, да и сделать иногда нельзя.
А вот да. Я постараюсь эту книжку купить,внуку подарить.
А вообще- это же базовые знания. Без базовых знаний нельзя нормально освоить современные технологии. Я тоже краем уха-уголком глаза пробегал мимо ВПК, меня это просто убивало: люди программу задают - "нажми на кнопку - получишь результат, твоя мечта осуществится", но они не понимают, что делают, если что-то не получилось, они не понимают, как выходить из ситуации. Где мог,просвещал молодых технологов, но это не восполняет системных пробелов в знаниях.
Эх, не находится к сожалению поиском в яндексе очерк "Критические точки его превосходительства", прочитанный мною в детстве в одной из емнип советской серии книг "Хочу все знать" или чего-то подобного, как раз про жизнь и работу Д.К. Чернова. Эти бы книжки подрастающему поколению читать, а не в тиктоках сидеть...
Так и напишите про суть легирования, про то, отчего легирующие элементы чем ниже по Периодинческой таблице - тем лучше легируют. Причем простыми словами.
Отчего в бронзу надо совать 15 процентов олова, или 5-6 мышьяка, или 2 - 3 урана для одинаковых механических свойств?
"дальше все автоматика и на компьютере можно все проследить. А так спасибо за ностальгию"
- ага, а я, когда столкнулся с изготовлением упора, где нужна закалка только с одной стороны - уперся в "новые технологии": либо делать специальный индуктор под упор (а он нужен только один - для ремонта станка), либо закалка всей детали "автоматическая, по компьютеру, с охлаждением жидким азотом". Пришлось обращаться к сельскому кузнецу ( в буквальном смысле - кузница 18-го века для туристов в баронском имении) - он все сделал в лучшем виде, как надо. Да, сталь была, если чо: ШХ15, а станок - итальянский.
Это веселая ситуация!
А я сейчас ищу, где бы закалить "ножики" для упаковочного станка, 400х50 мм габарит, по форме как буква Т с низкой ножкой (там крепление). У большинства ножеделов - печки по 320 мм и короче. А упаковочный станок "импортозамещенный", в отличие от итальянского, для подточить или заменить нож - разборка-сборка занимает полдня.
С институтского строймата по металлу в памяти только мартенсит и остался
Перлит, аустенит, мартенсит, ледебурит, феррит, цементит - это навскидку. Но это не всё.
Здравствуйте! Хорошая статья. Скажите а у вас можно заказать нож? Если да, то на каком ресурсе?
Можно. Отписал в личку.
Разобрано хорошо, но тема
сисеказотирования не раскрыта. Как Вы без этого хорошую сталь будете делать?Хотите разберу). 0,1 мм за 10 часов при идеальных условиях)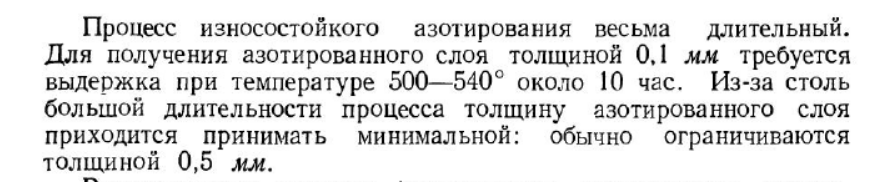
Не понятно где и как выдерживать. В какой среде. Азотировать можно по разному.
Давайте так, Вы это в следующей статье разберите. Ваша тема ведь. А азотирование стали - очень интересный процесс.
В следующей прода про закалку. Потом посмотрим)
Аммиак
По разному конечно можно азотировать. Но 80 процентов- газовое азотирование в аммиаке. Процентов 20 ионное. С ионным свои сложности большие( халаты белые, руки чистые, экраны в реторте специальны вокруг детали, но при хорошем оборудовании и очень квалифицированном персонале- результат неплохой) .
По моим опытам:
Смесь угольной пыли, карбамида и чуток соды. Карбамид растереть с немного угля, а потом перемешать с остальным количеством. Контейнер из простой стали, крышка на болтах, стык замазал "каминфикс"-ом. Клал контейнер в уже разогретую муфельную печь ПМ-8, регулятор на "7", цвет свечения между красным и оранжевым. Так как пирометра у меня нет :(. Время прогрева контейнера часа три. Да, из печки идет дымище! мастерская была сильно задымлена, пришлось открывать верхние окна для проветривания. Остывание с печью. Получается черный слой, блестящий. РФ-овский надфиль не берет, советский царапает. (твердомера у меня нет)
Кроме предмета, обрабатывал полоски 304-нержи для опыта. На изломе видно что мелко-мелко зернистый слой примерно половину мм.
Ну это зависит от цели( износостойкость, коррозионностойкость, износостойкость при высоких температурах и тд). А также и более чем от марки стали. На 12х18н10т вы при газовом азотировании 0,1 мм получите часов за 90. А на 20х25н19 скорее всего без добавки хлорида аммония в реторту не получите вообще. Если нужна эпсилон-фаза скажем на 09г2с или стали 45 , а это важно для гидроцилиндров- то только карбонитрирование, но вторым нагревом, а сначала азотирование при 520. Ну а на штамповых сталях ( 4х5мфс) 0,15 мм за 8 часов от пола до пола это можно
Во-во)
Ну, теперь то я наконец-то понял, как античные кузнецы изготавливали булат из криничного железа!
Они просто-напросто клали заготовку в огнеупорный тигель, засыпали графитом и ставили в электрическую муфельную печь на 3-4 часа!
Примерно так, только муфель заменяли пара-другая рабов на мехах. А тигли даже я леплю сам)
Вам известна муфелька на 1300+ градусофф?
У жены две, но макс- 800🤔.
А в остальм вы правы- так всё и было😁
Идете в сеть и ищите. Там и 1500 есть. Повторюсь: муфельную печь заменяла печь под тигли. Электричество и нагревательный элемент заменяли уголь и пара рабов на мехах для подачи воздуха. Я на угле жуть сколько стали переплавил, рабов у меня не было, но пылесос имелся.
" будем искать"(с)🙂
У меня " улитка" на поддуве, на 380 движ. Может и хватит.
А чего их искать, забиваете в поиск и выбираете. Правда цена иногда негуманная)
У меня такая есть, на ней кокс отлично работает.
Персидский уклад,вутц,индийский булат и тому подобные стали с нагревом от 1300+ известны давно.Там простая огнеупорная печь в форме купола,внуртях у ей тумба,на ей тигель с варевом.Суть что входной поток воздуха в самом низу,под углем,выхлопной чуть выше середины купола.Весь жар идет вверх для расплава содержимого тигля
Чуть горно " доработать" и ?( кирпича шамотного поддон в наличии😎.
Про якутский нож всё жду...
Будет. )
Страницы